一、低克度原紙帶來的問題
1、 Problems of low gram base paper
用低克度紙做瓦楞紙板面紙時,會出現(xiàn)瓦楞紙板表面顯坑紋的毛病。容易引起顯楞和在楞的低凹處印不出所需的圖文內(nèi)容,針對顯坑造成的瓦楞紙板表面不平整,應(yīng)選用回彈性較好的柔性樹脂版做印版,來克服印刷不清晰和露底的缺陷。尤其是用低克度紙生產(chǎn)出來的A型瓦楞紙板,經(jīng)印刷機(jī)印刷會使瓦楞紙板的平壓強(qiáng)度受到較大損傷,另外瓦楞紙板經(jīng)過印刷輥和壓印輥后,其邊壓強(qiáng)度也會有較大損傷。
When using low gram weight paper to make corrugated board face paper, there will be pit marks on the surface of corrugated board. It is easy to cause the corrugation and the required graphic content can not be printed on the low concave part of the ridge. In view of the uneven surface of the corrugated board caused by the pit, the flexible resin plate with good resilience should be selected as the printing plate to overcome the defects of unclear printing and exposure. In particular, the A-type corrugated board produced by low gram weight paper will be greatly damaged by printing press. In addition, the edge pressure strength of corrugated board will also be damaged after passing through printing roller and embossing roller.
如果瓦楞紙板的面紙和里紙克度相差太大,還容易導(dǎo)致瓦楞紙板線生產(chǎn)出的紙板出現(xiàn)彎曲。紙板彎翹對印刷會帶來套印不準(zhǔn)和印刷開槽走位現(xiàn)象,因此對彎翹紙板應(yīng)采取壓平后再印。如果強(qiáng)行印刷不平整的瓦楞紙板容易引起走位。也會影響瓦楞紙板的厚度下降。
If the difference between the surface paper and the inner paper of corrugated board is too big, it is easy to lead to the bending of the cardboard produced by the corrugated board line. The warping of paperboard will lead to overprint inaccuracy and printing slotting, so the warped paperboard should be flattened before reprinting. If forced printing uneven corrugated board, easy to cause displacement. Can also affect the thickness of corrugated board.
二、原紙表面粗糙度不同帶來的問題
2、 Problems caused by different surface roughness of base paper
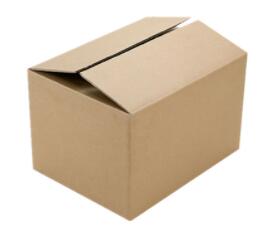
在表面粗糙、纖維明顯的原紙上印刷,其油墨的滲透性大,印刷墨跡干燥快,而在表面平滑度高、纖維質(zhì)密堅韌的紙上印刷,其墨跡的干燥速度慢。因此在較粗糙的紙張上,應(yīng)加大施墨量,在表面平滑的紙張上應(yīng)減少施墨量。在沒有施膠的紙上印刷墨跡干燥快,而在經(jīng)過施膠的紙上印刷墨跡干燥慢,但印刷圖案的再現(xiàn)性好。如涂布白板紙因吸墨性比箱板紙、茶板紙小,墨跡干燥慢,而平滑度又比箱板紙、掛面紙、茶板紙高,因此,在其上面印刷細(xì)小網(wǎng)點的分辨率也高,其圖案的再現(xiàn)性也比掛面紙、箱板紙、茶板紙要好。
When printing on base paper with rough surface and obvious fiber, the ink permeability is large and the ink drying speed is fast, while the ink drying speed is slow when printing on paper with high surface smoothness and dense and tough fiber. Therefore, in the rough paper, the amount of ink should be increased, and on the paper with smooth surface, the amount of ink should be reduced. The ink drying on the paper without sizing is fast, while that on the paper after sizing is slow, but the printing pattern has good reproducibility. For example, because the ink absorption of coated white board paper is smaller than that of box board paper and tea board paper, the ink drying is slow, and the smoothness is higher than that of box board paper, hanging paper and tea board paper. Therefore, the resolution of printing small dots on it is also high, and the reproducibility of its patterns is better than that of hanging paper, box board paper and tea board paper.
三、原紙吸收差異帶來的問題
3、 Problems caused by the difference of base paper absorption
由于造紙原料的差異和原紙施膠、壓光、涂布的差異,在吸收性能方面就不同,如在單面涂布白板紙和牛皮卡上進(jìn)行疊印時,因吸收性能低,墨的干燥速度就慢一些,所以應(yīng)降低前一道水墨的濃度,提高后面疊印水墨的粘度。并將線條、文字、小圖案放在色印刷,把滿版實地放在一色印刷,這樣可以提高疊印效果,另外把深顏色的放在前面印,把淺顏色的放在后面印,可以遮蓋套印誤差,因為深色覆蓋力強(qiáng),有利于套印標(biāo)準(zhǔn),而淺色覆蓋能力弱,放在后面印即便有跑位現(xiàn)象也不容易觀察出來。
Due to the difference of papermaking raw materials and the difference of sizing, calendering and coating of base paper, the absorption performance is different. For example, when overprinting on single-sided coated white board paper and pickup, the drying speed of ink is slower due to low absorption performance. Therefore, the consistency of the previous ink should be reduced and the viscosity of the later overprint ink should be increased. The lines, characters and small patterns are printed in the first color, and the full page is printed in the last color, which can improve the overprint effect. In addition, the dark color is printed in front of the printing, and the light color is printed in the back, which can cover the overprint error. Because of the strong coverage of the dark color, it is conducive to the overprint standard, while the light color coverage is weak, even if there is run-off phenomenon in the back printing It's not easy to see.
原紙表面的施膠狀況不同也會影響對墨跡的吸收量。施膠量小的紙吸墨多,施膠量大的紙吸墨少,所以應(yīng)根據(jù)紙的施膠狀態(tài),調(diào)整各墨輥的間隙,也就是調(diào)小各墨輥的間隙,來控制印版的著墨量。由此可見,原紙入廠時應(yīng)對原紙的吸收性能狀況進(jìn)行檢測,并給印刷開槽機(jī)和配墨人員一個原紙的吸收性能參數(shù),以便于他們配墨和調(diào)整設(shè)備。并針對不同原紙的吸收狀態(tài),調(diào)整墨的粘度和PH值。
Different sizing conditions on the surface of base paper will also affect the amount of ink absorption. The paper with small sizing amount absorbs more ink, while the paper with large sizing amount absorbs less ink. Therefore, according to the sizing state of the paper, the gap of each ink roller should be adjusted, that is to say, the gap of each ink roller is adjusted to control the ink amount of printing plate. It can be seen that when the base paper enters the factory, the absorption performance of the base paper should be tested, and a parameter of the absorption performance of the base paper should be given to the printing slotting machine and ink dispensing personnel, so as to facilitate their ink mixing and equipment adjustment. According to the absorption state of different base paper, the viscosity and pH value of ink are adjusted.
Today, I'd like to introduce to you the relevant knowledge of corrugated box manufacturers. For more wonderful contents, please click our website: http://spotifyhits.com We will have more knowledge for you.